In today’s competitive marketplace, the speed and accuracy of order fulfillment can be the difference between a thriving business and one that struggles to keep up.
E-commerce growth, coupled with heightened customer expectations for rapid delivery, has made optimizing warehouse layouts more critical than ever. Efficient warehouse design not only improves order picking speed but also reduces operational costs, minimizes errors, and boosts overall productivity. This guide provides in-depth tips and strategies to help you optimize your warehouse layout for faster and more accurate fulfillment.
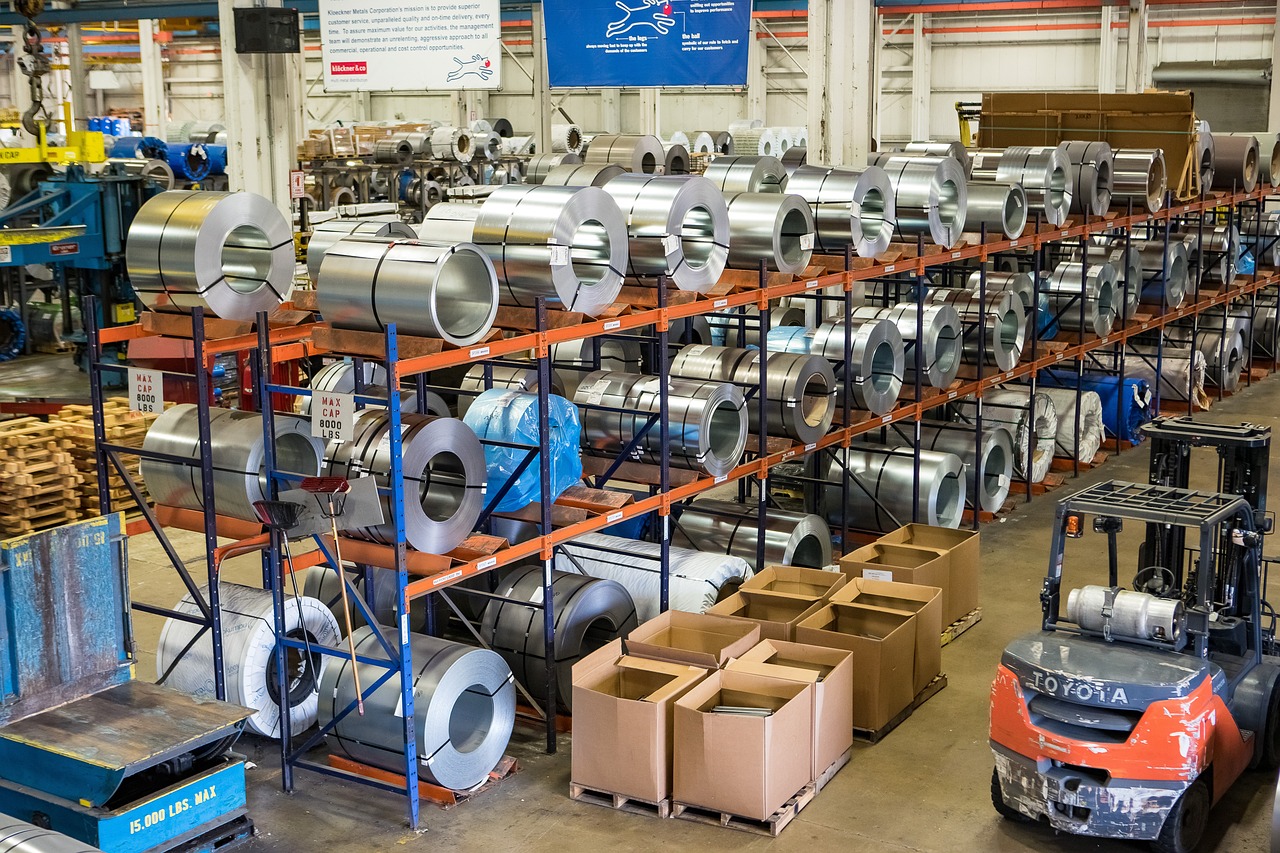
1. Understand Your Product Flow
One of the foundational steps in optimizing your warehouse layout is understanding the flow of products. This involves analyzing how items move through your warehouse from the moment they arrive until they are shipped out.
- Analyze Movement Patterns: Begin by mapping out the movement patterns of your most frequently picked items. Place high-demand products closer to the packing and shipping areas. This reduces travel time and speeds up the picking process. By placing frequently accessed items in easily reachable locations, you can minimize travel distances and improve overall efficiency (FCBCO).
- ABC Analysis: Implement the ABC analysis method to categorize your inventory based on demand frequency. ‘A’ items are high-demand, ‘B’ items are moderate-demand, and ‘C’ items are low-demand. Store ‘A’ items in the most accessible locations, closest to the dispatch area, while ‘C’ items can be placed further away. This strategy ensures that your most frequently picked items are the easiest to access, thereby speeding up order fulfillment.
2. Implement a Logical Zoning System
Zoning your warehouse into specific functional areas is another critical step in improving efficiency. Clearly defined zones reduce confusion and help workers navigate the warehouse more effectively.
- Create Functional Zones: Divide your warehouse into zones for receiving, storage, picking, packing, and shipping. Each zone should have a clear purpose and layout to support that purpose. For instance, the picking zone should be strategically located to minimize travel time between picking and packing (FCBCO).
- Cross-Docking Areas: For high-turnover products, consider setting up cross-docking areas where goods can be directly transferred from receiving to shipping without long-term storage. Cross-docking not only speeds up the fulfillment process but also reduces the need for storage space, which can be a significant cost-saving measure (FulfillmentIQ).
3. Optimize Aisle Widths and Layout
The layout of your warehouse aisles plays a crucial role in determining the speed and efficiency of order fulfillment.
- Adjust Aisle Widths: The width of your aisles should be determined by the type of equipment used and the traffic patterns within your warehouse. Wider aisles are necessary for areas with heavy forklift traffic, while narrower aisles may suffice in areas where only manual picking occurs. Optimizing aisle widths can improve space utilization and enhance the overall efficiency of warehouse operations (NetSuite).
- Adopt a U-Shaped Layout: For many warehouses, a U-shaped layout is highly effective. This layout allows for smooth flow from receiving to shipping, with minimal backtracking. It also centralizes key operations like picking, packing, and shipping, reducing the distance that workers need to travel (FCBCO).
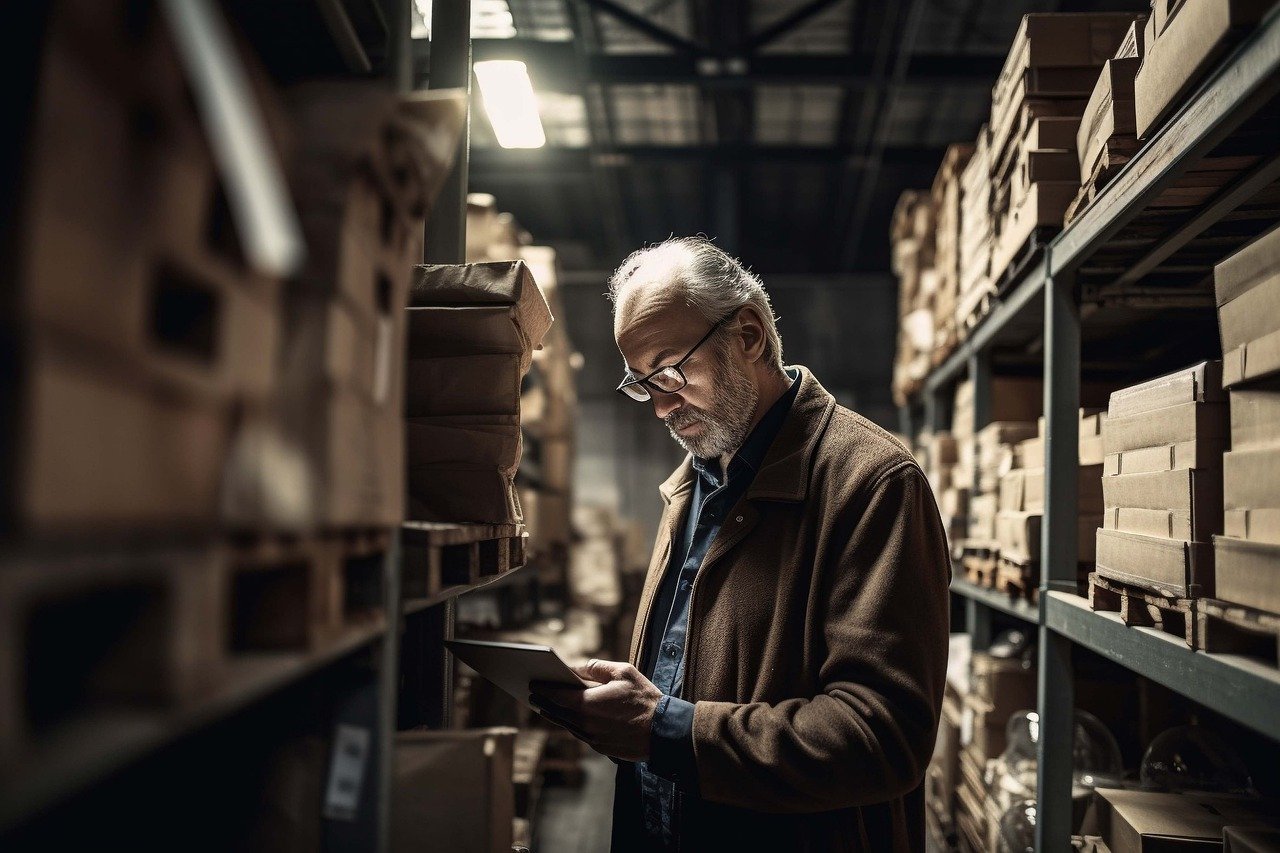
4. Use Vertical Space Effectively
Vertical space is often underutilized in warehouses, but with the right approach, it can significantly increase your storage capacity without expanding your warehouse footprint.
- Install High-Density Storage Systems: Utilize vertical space by installing high-density storage systems, such as pallet racking or multi-tier shelving units. These systems allow you to store more products in the same footprint, which is particularly useful in smaller warehouses (FCBCO).
- Automated Storage Solutions: For high-volume SKUs, consider investing in automated storage and retrieval systems (AS/RS). These systems use robotics to retrieve items from high-density storage areas, reducing retrieval time and improving picking accuracy. This approach is supported by studies that show significant improvements in order picking times when using automated systems(NetSuite).
5. Implement Pick Path Optimization
Pick path optimization is crucial for reducing the time it takes to fulfill orders. By optimizing the routes that workers take to pick items, you can significantly improve efficiency.
- Use Batch Picking: Batch picking involves grouping orders together and picking all items for those orders in one pass through the warehouse. This minimizes travel distance and reduces picking time, especially for smaller orders. Batch picking is particularly effective in environments where there is a high volume of small orders (FulfillmentIQ).
- Wave Picking: In larger warehouses, wave picking can be a game-changer. This method involves organizing picking activities into waves or batches based on factors like order urgency, shipping schedules, or product type. Wave picking allows you to optimize the picking process for specific criteria, making it faster and more efficient (NetSuite).
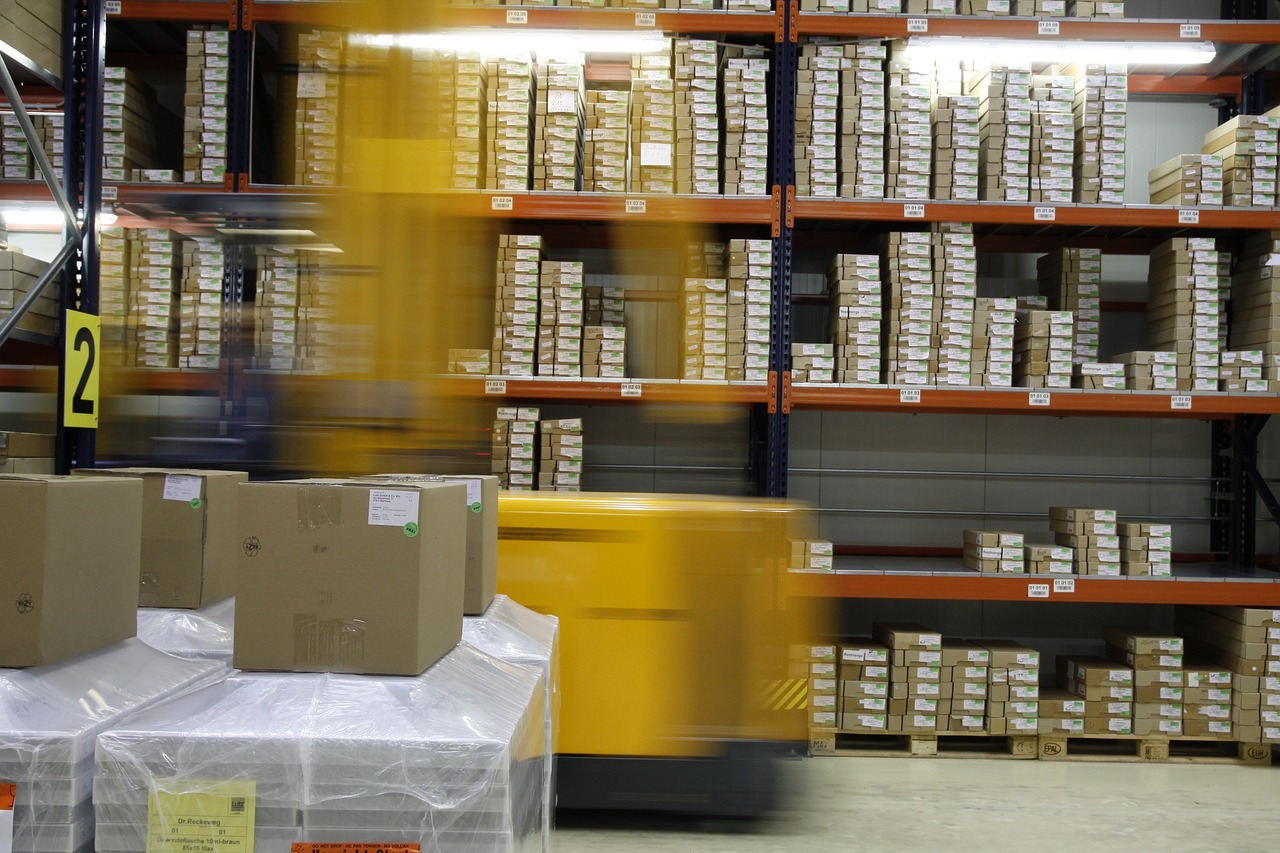
6. Leverage Technology for Real-Time Insights
Technology plays a pivotal role in modern warehouse management, providing the real-time data needed to optimize operations.
- Warehouse Management Systems (WMS): A robust WMS is essential for any warehouse aiming to improve efficiency. A WMS provides real-time data on inventory levels, order status, and pick paths, enabling workers to make informed decisions quickly. With features like slotting optimization, a WMS can automatically assign the best locations for products based on picking frequency, reducing travel time and increasing picking speed (FCBCO).
- Barcode Scanning and RFID: Implementing barcode scanning or RFID technology allows for real-time tracking of inventory movement. These technologies not only reduce human error but also speed up the picking process by providing instant access to product information (NetSuite).
7. Continuous Improvement Through Data Analysis
Optimizing your warehouse layout is not a one-time task. It requires ongoing analysis and adjustments to stay efficient and effective.
- Regular Audits: Conduct regular audits of your warehouse layout and processes to identify bottlenecks, inefficiencies, and areas for improvement. Use data collected from your WMS and other technologies to make informed decisions about layout.
8. Prioritize Safety
While optimizing for speed and efficiency, it’s important not to overlook safety. A safe warehouse is not only a legal requirement but also contributes to smoother operations.
- Clear Signage and Pathways: Ensure all zones and aisles are clearly labeled with signage to guide workers and prevent confusion. This is especially important in large warehouses where it’s easy for workers to get disoriented. Adequate lighting and clearly marked paths contribute to a safer and more efficient environment (NetSuite).
- Safe Traffic Flow: Designate specific pathways for equipment and personnel to prevent accidents and ensure smooth traffic flow within the warehouse. This includes marking pedestrian walkways and forklift lanes clearly. Proper safety protocols and regular training sessions are essential to maintain a safe working environment (FCBCO).
Conclusion
Optimizing your warehouse layout for faster fulfillment is a multifaceted process that involves strategic planning, technology integration, and continuous improvement. By understanding your product flow, implementing a logical zoning system, optimizing aisle layouts, and making effective use of vertical space, you can significantly enhance the speed and accuracy of your order fulfillment processes.
Moreover, leveraging technology like WMS and RFID, combined with strategies like pick path optimization and batch picking, can further streamline operations and reduce errors. Continuous monitoring and improvement, along with prioritizing safety, ensure that your warehouse remains efficient and productive in the long term.
In an increasingly competitive market, these optimizations are not just about improving efficiency—they are about staying ahead of the curve and meeting customer expectations for rapid, accurate order fulfillment. By investing in these strategies, you position your warehouse for success now and in the future.
References:
- “Warehouse Layout Optimization Tips,” FulfillmentIQ. Available at FulfillmentIQ (FulfillmentIQ).
- “12 Tips for Warehouse Layout Efficiency,” NetSuite. Available at NetSuite (NetSuite).
- “15 Operational Ideas for Optimizing Warehouse Layouts and Processes,” F. Curtis Barry & Company. Available at F. Curtis Barry & Company (FCBCO).
Recent Comments