Many businesses struggle to optimize their warehouse operations due to their reliance on manual workflow processes. From order management to inventory control, many businesses believe that adding more staff to handle the increased workload is the easiest way to scale operations and meet growing customer demands. However, this approach introduces several challenges that can limit productivity and hinder long-term growth.
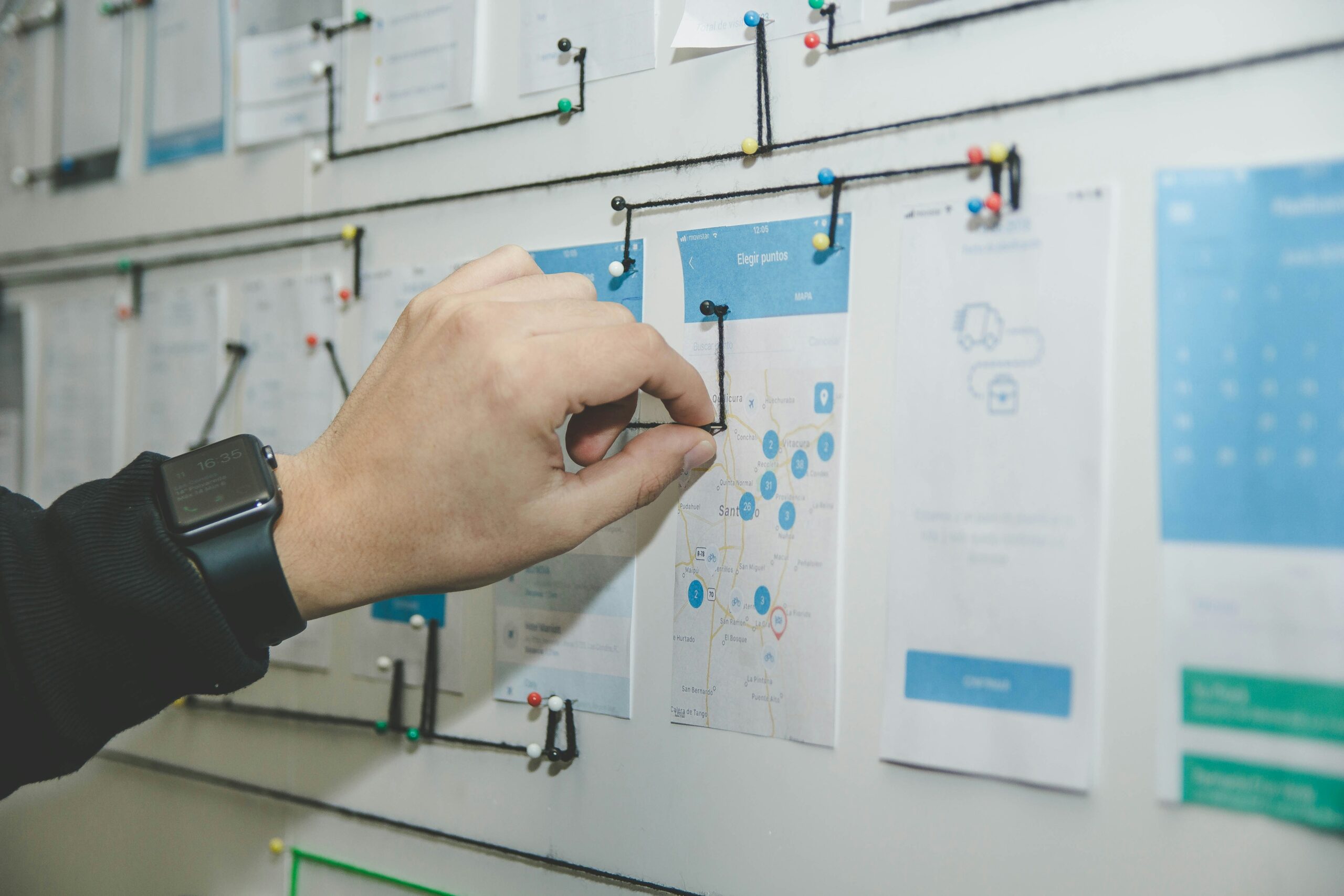
The Pitfalls of a Lack of Software Integration
- Increased Workload: As customer demand rises, manual workflows place additional strain on staff, often leading to the need for more hires. This drives up labor costs, but the productivity gains remain minimal.
- Higher Risk of Errors: Manual data entry and disjointed workflows create a higher risk of errors in the fulfillment process. Incorrect inventory counts, misrouted shipments, and missed orders can lead to customer dissatisfaction and costly returns or chargebacks.
- Scalability Issues: Manual workflows limit a business’s ability to scale effectively. As order volume grows, the lack of automation creates bottlenecks that hinder efficiency and lead to delayed shipments, negatively impacting customer experience.
- Fragmented Systems: Without an integrated system, accounting, inventory, and warehouse management operate in isolation. This fragmentation makes it challenging to track the progress of orders, invoices, and inventory levels across departments, resulting in inconsistencies and delays.
A Better Way Forward: Leveraging a WMS with Integrations
Instead of relying on manual workflows, businesses can streamline their operations and reduce costs by implementing a Warehouse Management System (WMS) with integrations. A WMS provides seamless integration between various software platforms, centralizing critical functions and improving data accuracy. How can an integrated WMS can transform warehouse management?
- Automating workflows through an integrated Warehouse Management System (WMS) significantly streamlines the entire process from order creation to shipping and billing. This automation minimizes manual data entry, thereby ensuring that all departments are working with accurate and up-to-date information. By simplifying these processes, businesses can boost efficiency and reduce the likelihood of errors.
Real-time data synchronization is another key feature of an effective WMS. By integrating with accounting, Enterprise Resource Planning (ERP), and e-commerce platforms, the system synchronizes data instantly. This crucial capability ensures consistency across various systems and provides all stakeholders with the most current information, facilitating better decision-making and operational alignment.
Centralized management is facilitated by having all critical data accessible from a single system. This consolidation allows businesses to track orders, monitor inventory levels, and generate invoices efficiently, without the need to juggle multiple software tools. For even greater flexibility, cloud-based solutions like K.Motion Edge offer the added advantage of providing real-time warehouse insights from any location, enhancing visibility for remote managers or teams.
Scalability is a fundamental aspect of an integrated WMS. As a business grows, whether through increased order volumes or the addition of new distribution channels, a robust WMS can adapt seamlessly. This adaptability ensures that businesses can expand without the need for major workflow alterations or system overhauls, supporting sustained growth with the existing infrastructure.
Lastly, by automating repetitive tasks and centralizing data management, a WMS significantly reduces the need for additional warehouse or administrative staff. This not only helps in controlling labor costs but also maintains or enhances productivity levels. Through these efficiencies, businesses can allocate resources more strategically, focusing on growth and innovation rather than routine tasks.
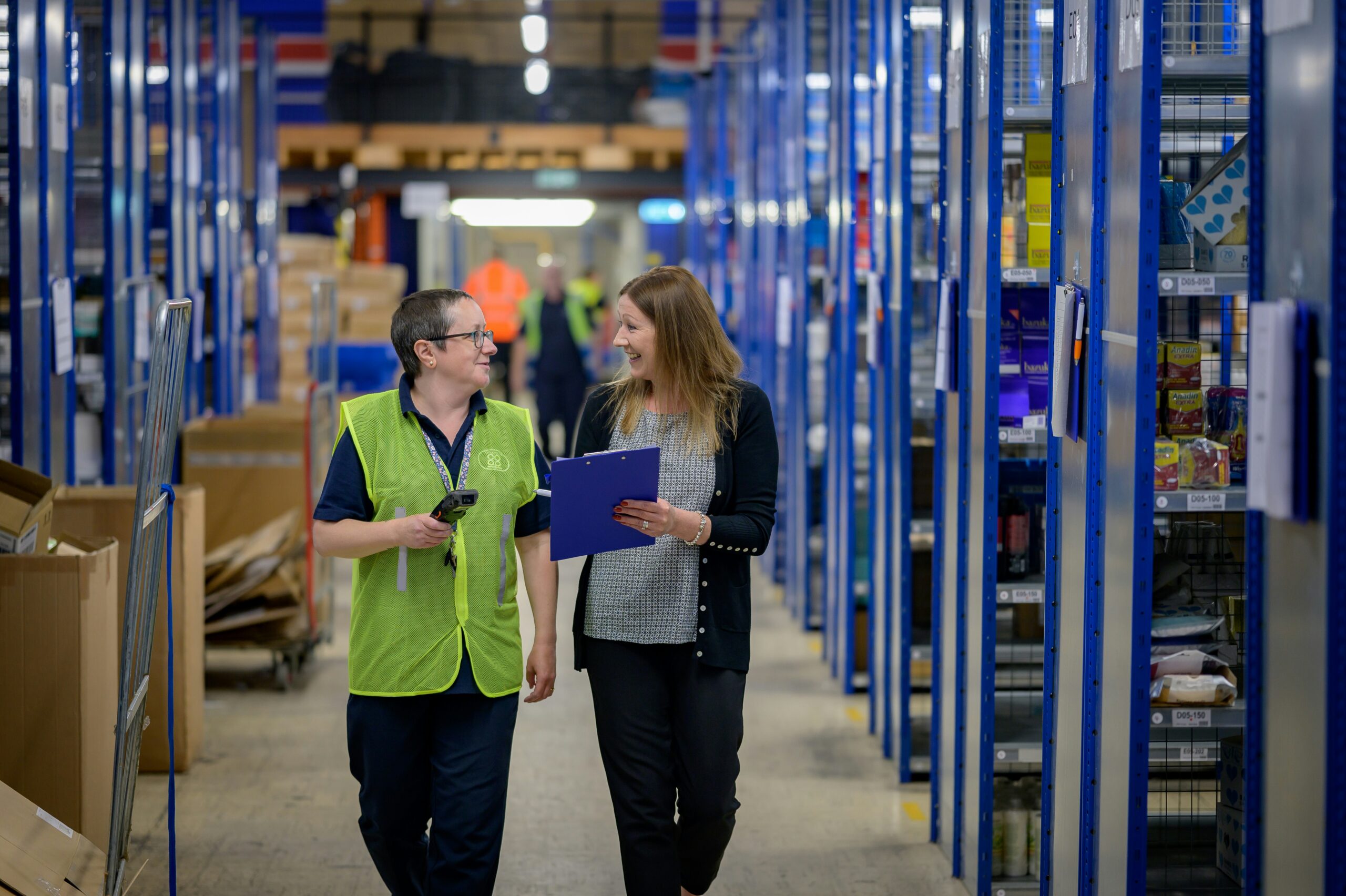
The Benefits of Integrated Solutions for Your Business
An integrated Warehouse Management System isn’t just a tool; it’s a strategic asset that can unlock new opportunities for growth while minimizing operational risks. Here’s why your business should consider implementing a WMS:
- Cost Savings: By automating manual tasks and reducing the need for additional staff, a WMS can lower overall labor costs. Centralized data management also minimizes the risks of chargebacks, returns, and inventory losses.
- Better Decision Making: Real-time data synchronization provides accurate insights into your business’s operations, allowing for informed decision-making. Managers can proactively adjust workflows, predict future trends, and identify areas for process improvement.
- Increased Customer Satisfaction: Meeting customer expectations is crucial to building brand loyalty. An integrated WMS ensures that orders are processed correctly, inventory levels remain accurate, and shipments arrive on time.
- Future-Proof Scalability: As your business grows, a WMS can adapt to new challenges, including increased order volume, expanded product lines, or new customer requirements.
In Conclusion: The Power of Software Integration
Businesses that rely on manual workflows often face rising labor costs, data inconsistencies, and operational bottlenecks that limit growth. By implementing a Warehouse Management System with seamless integrations, companies can streamline workflows, improve data accuracy, and scale efficiently.
Supplysoft’s integrated WMS solutions powered by Körber are designed to help small and medium-sized businesses achieve greater efficiency, accuracy, and customer satisfaction. With our expertise in software integration, we can help your business unlock the power of automation and transform your warehouse operations. Contact Supplysoft today to learn how an integrated WMS can provide the seamless solution your business needs to thrive.
Recent Comments